360° PLANNING AND CO-DESIGN
Production of moulds and dies for die castings.
For each project involving a new Aluminium and Zamak die casting, La Cibek die casting provides a filling simulation of the casting using CASTLE software, which allows possible criticalities to be identified and resolved before the tooling is made. This significantly reduces both the start-up time of a new project and the cost of tooling changes after the first mould test.
ATTENTION TO EVERY DETAIL
La Cibek die casting has always paid great attention to the quality of the tooling to be manufactured, quality that is never detached from special attention to containing mould costs.
In order to contain tooling costs, for die castings involving very limited quantities very limited production quantities, prototype moulds are made.
The quality of mould, construction is ensured with the help of a network of long-term specialized partners.
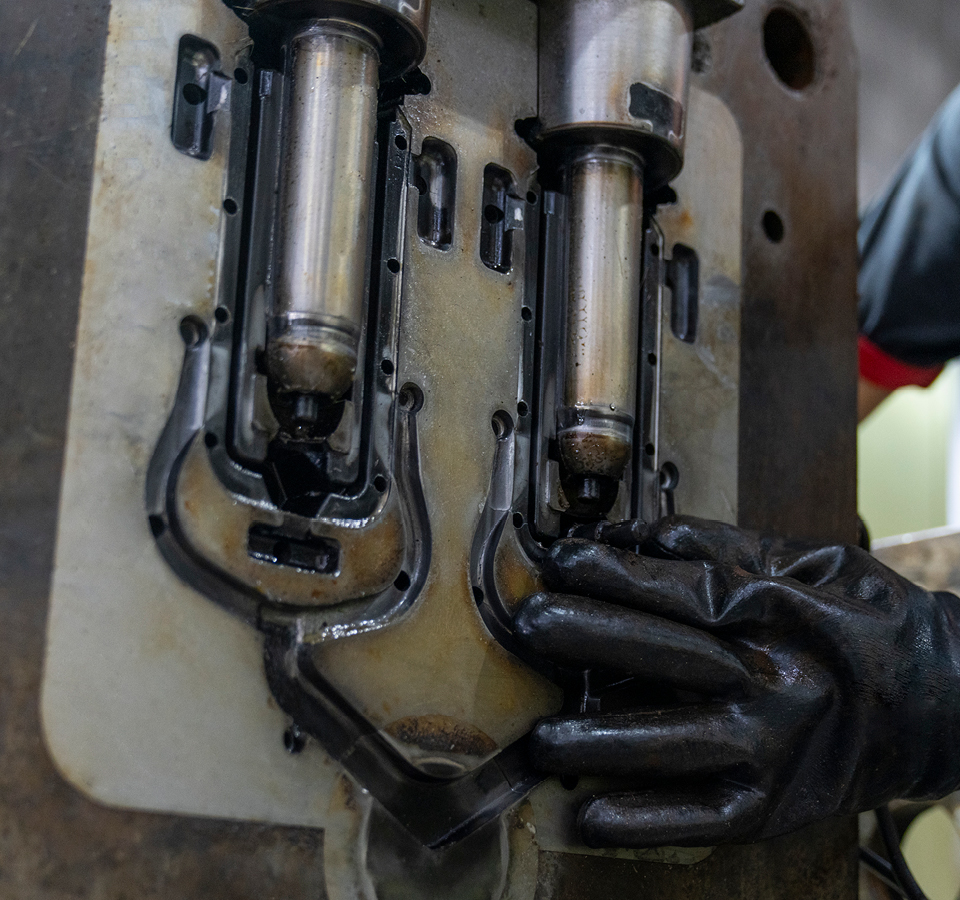
Reverse Engineering Services
With a view to production continuity, La Cibek die casting is able to provide both ordinary mould maintenance services, i.e. the simple replacement of some of its worn parts, and a complete Reverse Engineering service on a mould supplied by a third party.
On this basis, the company is able to provide a feasibility study and costs for an extraordinary maintenance or redesign of the mould, even in the complete absence of project documentation.
Lead times
An order of magnitude of the lead time for production and delivery of a mould from the “Final drawing validated by the customer” are 30 to 60 working days depending on the size and complexity of the tool to be made.
La Cibek die casting performs a ‘prompt delivery‘ service for parts for which a ‘final drawing’ has been agreed in advance with the customer for an authorized stock lot.
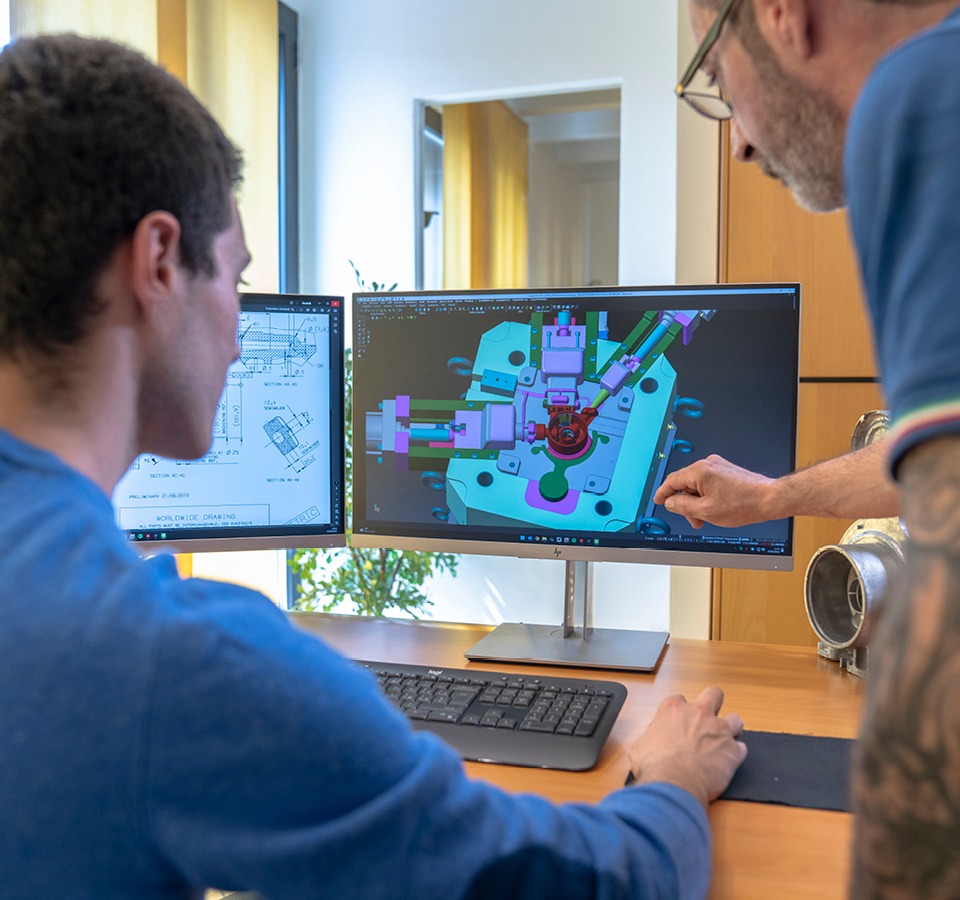
– QUICK AND PRECISE ANSWERS –
Management system (ERP)
The management system (ERP), which is also fully integrated with the production control and management part, makes it possible to know “in real time” the number of Aluminium and Zamak parts produced by the presses and to know the stage of processing they are in. This allows a rapid and precise the customer at all times, particularly on:
-
- The status of a current order;
- The shortest delivery date for any new order, taking into account lead-time and actual workloads of the machines.
– CONTACT US –